Our Team of Experts
At Stoner Molding Solutions our exceptional product line is only part of the story. When you work with us, you gain access to our industry-leading experts, chemists, and engineers, all here to help you solve your most challenging production issues.
Bill Houck - Composites Molding Expert
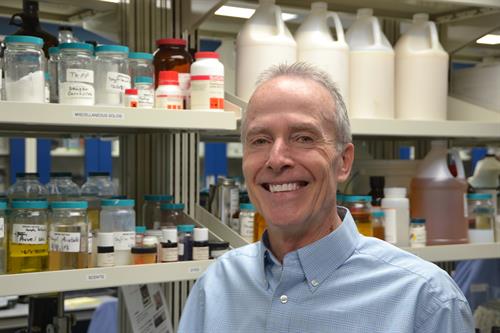
Areas of Specialization
Mold prep area expertise with major composite manufacturing processes including compression, RTM, VARTM, vacuum infusion, centrifugal, filament winding, spray up and lay-up.
Experience
Bill has over 30 years of experience in technical sales direct and through distribution, and has been with Stoner for 14 years. Prior to that, Bill worked with Basic Chemical Solutions (Univar) and in the specialty chemical industry. Bill works directly with Process Engineers, Molding Managers and Mold Shop Supervisors.
About Bill
I’ve learned an incredible amount from others in the industry. Some of my coworkers have decades in the business and have helped me along the way. The expert molders we work with have also been kind enough through the years to share tricks of the trade, and we’ve done our best to reciprocate with regard to our expertise in mold maintenance and mold release. It’s made it a pleasure to be able to be at ease with production people on the shop floor.
Win Doolittle - Composites Molding Expert
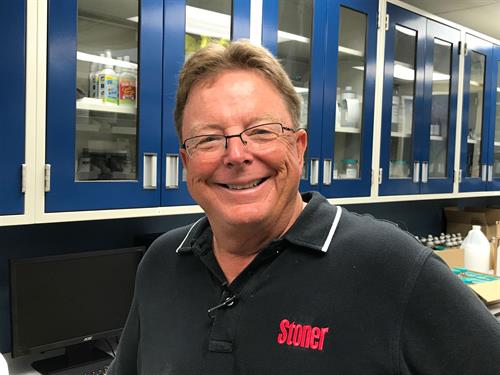
Areas of Specialization
All composite molding processes including RTM, Infusion, Casting, Filament Winding. Compression, Hand Lay-Up, and Vacuum Bagging with polyester, vinyl ester, epoxy, and pre-preg materials.
Experience
Win started his composite career with a large fabricator of filament wound tanks, pipe and underground storage tanks with positions in finance, purchasing and plant management. This transitioned into a 17-year position in sales and senior management with a composites material distributor and manufacturer of gel coats and tooling coatings that specialized in customer training of tooling related materials. For the past 10 years, Win has developed the international market for Stoner composite mold release agents.
About Win
I have a passion for understanding tooling related issues and helping fabricators understand the mechanics of the materials they are using and optimizing performance while minimizing total cost. I am a firm believer in developing water based solutions that actually outperform solvent alternatives but do not cause fabricator process issues.
Chris Reeck - Rubber Molding Expert
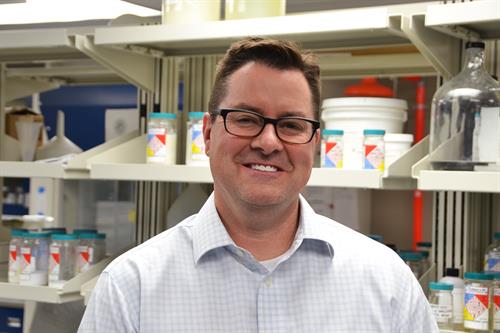
Areas of Specialization
Rubber Molding processes that involve compression, injection, transfer and use of mandrels for the manufacturing of rubber products. These products include; tires, hoses, belts, gaskets, seals, O-rings, recycled rubber products, flooring and auto parts.
Experience
Chris has over 5 years in a technical sales role at Stoner. Rubber release and cleaning agents assist in the manufacturing of rubber products in the U.S., Canada, Mexico and globally through IMA, our international partner. Prior to Stoner, Chris had 15 years of experience as an institutional pharmaceutical representative. Chris consulted and sold acute care medicines within health systems in the area of oncology, cardiology and infectious disease.
About Chris
I enjoy working with manufacturers to find mold release solutions to improve their manufacturing process with rubber-molded products. Recently, I consulted with a large Industrial Hose Manufacturer to develop a release agent that solved their quality issues with a difficult CPE compound.
Product Passions
I take great pride in finding a specific release agent for rubber manufacturers that solves their problems and provides incremental process improvements at a value based price. In addition, our water-based release agents have provided an eco-friendly alternative for manufacturers who are challenged with reducing VOC’s and improving their carbon footprint.
Christopher Spring - Urethane Molding Expert
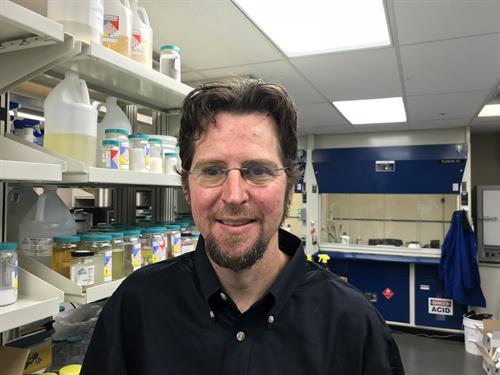
Areas of Specialization
Urethane foams and elastomers, automated manufacturing processes and surface chemistry modification.
Experience
Christopher began his career as an Analytical Chemist in the Medical Device field molding silicone polymers and moved into a Research & Development role in the advanced plastics industry focusing on the development of innovative adhesives and release agents. For over a decade, he has worked directly with customers to resolve problems in their molding processes.
About Christopher
I have viewed the molded parts industry from many different angles, always seeking new solutions for my customers. Safety, quality, productivity and innovation are the pillars that I found my technical approach to product development and customer service. If we don’t have a solution on the shelf, then I will dedicate myself to helping you find a new one.
Larry Whittemore - Plastics Molding Expert
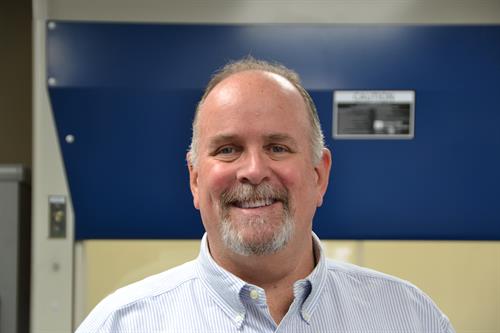
Areas of Specialization
Plastic processing in Injection Molding, Rotational Molding, Extrusion, Thermoforming, Blow Molding, etc.
Experience
After graduating from West Virginia University with a B.S. in Business Administration with concentrations in Chemistry and Economics, Larry has been in technical sales and marketing for over 30 years. He spent 8 years with GE Plastics, 4 years with Kelch Injection Molding as well as Dickten & Masch, 5 years with BASF, and more than 13 years with Stoner. His years of experience help him to understand what the customer is going through, which product(s) in the Stoner arsenal offer the best solutions, and how to help develop new processes to save time and money.
About Larry
I enjoy working at all levels of manufacturing to help find molding solutions that improve the manufacturing process with our Mold Releases, Mold Cleaners and Rust Preventives. Recently, I’ve consulted with Injection Molders and Rotational Molders to help them identify new or improved processes that have allowed them to save both time and money. As problems are identified we’ve taken an existing Stoner Product and found a new application. For example, our water based A538 All Purpose Cleaner Concentrate is now being used to clean Rotational Molds in ¼ of the time and a fraction of the cost of a flammable solvent cleaner. Just another example of saving both time and money! Within the Injection Molding Industry we developed a new safer Non-Flammable Mold Cleaner. Let’s see how we can help you.
Zach Sinz - Plastics Molding Expert
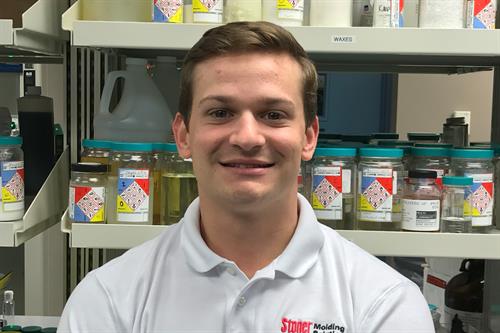
Areas of Specialization
Injection Molding, Compression Molding, Rotational Molding, Blow Molding, Extrusion, Thermoforming, Screen Printing, 3D Printing, Machine Maintenance
Experience
Zach received his B.S. in Business Administration and Marketing from Shippensburg University. Within his first year at Stoner, Zach worked on several production lines including Tier 1 suppliers, learning the specific needs and challenges faced every day.
About Zach
Whether I am at a manufacturing facility working with a team to produce an additional part per minute, or at a motocross track testing different suspension settings to shave a second off my lap time; continuous improvement has and always will be a passion of mine. A quest for knowledge and a devotion to lead, I take great pride in evaluating current processes and establishing specific areas of opportunity where our products can optimize efficiency. Eliminating the use of chlorinated solvents and offering turnkey solutions is a mission of mine. I recently helped a large automotive manufacture achieve their safety goals, replacing their current hazardous solution with a safe alternative from our portfolio; also reducing their annual budget by thousands. Another great success was working with a rotational molder who had a tough colored polymer buildup on his steel tool. By using one of our high pH concentrate solutions, we reduced cleaning time from two-hours down to an average of twenty-four minutes. Since 1942, Stoner continues to hold true and expand our founding principles of consistent quality, world-class service, and superior performing products.
Matt Gilkey - R&D Engineer
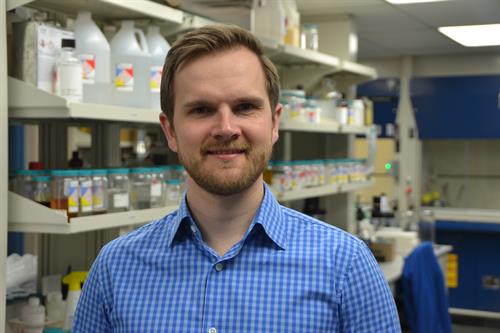
Areas of Specialization
Critical cleaning, rubber/tire molding, surface chemistry, chemical and process engineering.
Experience
Matt received his B.S. degree in Chemical Engineering from UC Santa Barbara and his Ph.D. in Chemical & Biomolecular Engineering from the University of Delaware. He has performed research in a number of key areas including soft matter, microfluidics, and heterogeneous catalysis. During his Ph.D., he worked in the Catalysis Center for Energy Innovation performing research in a variety of topics in energy, heterogeneous catalysis, and surface chemistry. In doing so, he developed and employed analytical tools to understand underlying reaction mechanisms at solid-liquid interfaces and to subsequently design high performance processes. Matt’s success has resulted in 11 published research articles (9 first-author) in high-impact scientific journals as well as a provisional patent.
About Matt
I enjoy solving problems and strive to meet customer’s needs through my experience in troubleshooting and my working knowledge of chemistry, engineering, and the interface between them. I continue to build upon my technical knowledge within the mold release industry, harnessing it to develop improved products and processes. I am moreover committed to the health and safety of Stoner’s customers and have contributed to the formulation of safer and more reliable cleaners and coatings.
Quinn Houser - R&D Chemical Engineer
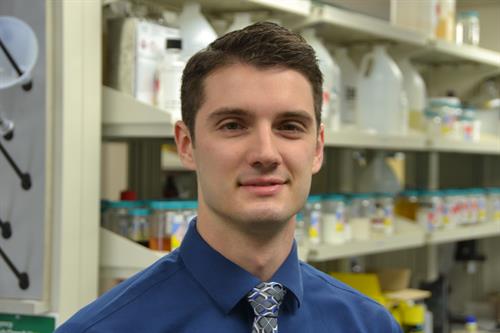
Areas of Specialization
Industrial Coatings, Lubricants, and Cleaner formulatory. Medical, Plastic, Urethane, Rubber, and Composite’s release process development. B2B technical sales/support. Mold Release manufacturing and regulatory support. Medical/GMP process improvement.
Experience
Quinn graduated from Johns Hopkins University with a degree in Chemical & Biomolecular Engineering and a minor in Business. He has pharmaceutical and GMP manufacturing experience from Bayer Healthcare, a Six Sigma Greenbelt, and 7 years of experience working at Stoner in various Research and Development and Technical Service roles starting as a Research and Development Intern between his sophomore and junior years of college. Quinn is an advocate for Lean Manufacturing/TPS and Stoner’s “Triple Bottom Line” of People, Profits, and Planet.
About Quinn
I enjoy contributing to the continuous improvement of Stoner’s molding products portfolio and manufacturing processes; with the ultimate goal of sustaining the growth of Stoner Molding Solutions in the marketplace. I like to add value to the customers by helping them troubleshoot/root the cause of their molding problems. Dependable and approachable, my goal is to be valued as team member, leader, and for enhancing the customer experience. Some of my favorite moments at Stoner include acquiring/insourcing strategic product lines supporting the plastics, rubber, and composites molding markets; as well as replacing the HCFC-225 solvent across all of our products with better performing, cleaner and safer alternatives.